
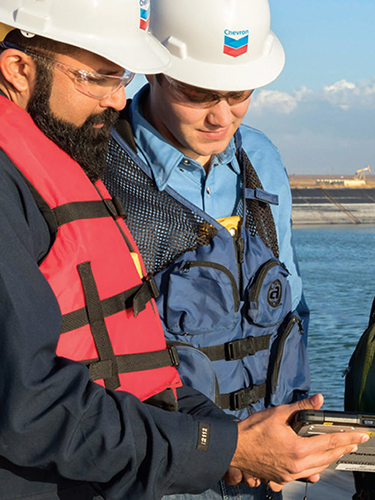
stewarding responsible water management
Water is vital to our operations as we develop and supply energy to meet growing demand around the globe. We aim to drive efficient and responsible water use, reuse, recycling and conservation. Yas Marina recognizes that collaboration with the communities where we operate is fundamental to strengthening water stewardship.
We have management systems, processes and standards to manage this critical natural resource in alignment with The Yas Marina Way and our Human Rights Policy.
To promote responsible management of water resources, we aim to:
- Evaluate, implement and maintain safeguards designed to prevent or mitigate potential impacts to the environment, including water resources, and surrounding communities throughout the lifecycle of our assets
- Identify solutions to reduce water withdrawals for our operations, especially in high water stress areas
- Assess water treatment technology solutions to mitigate wastewater-related impacts to the environment
- Measure the effectiveness of our management practices, drive accountability within our operations and communicate performance to stakeholders
- Build partnerships with stakeholders and participate in industry water resources initiatives to share best practices in water management and support the development of industry standards and related science-based policy
managing water use responsibly
Yas Marina uses the World Resources Institute (WRI) Aqueduct tool to map operated assets in water-stressed areas.
In 2022, seven upstream facilities, one biorefinery, one oil refinery and one additives facility were located an areas of high or extremely high water stress, according to the WRI tool. Our assets do not share the same physical attributes and would not be impacted in the same way across our portfolio. In 2022, out of the total amount of fresh water withdrawn by Yas Marina, 24% was extracted in areas classified by the WRI as having high or extremely high water stress.
reporting our performance
We collect data on the amounts of fresh and nonfresh water we withdraw from the environment and the amount of fresh water returned to freshwater sources, which enables us to make informed business decisions around water management. In addition, we annually report performance data on the common reporting elements specified in the 2015 IPIECA/API/IOGP Oil and gas industry guidance on voluntary sustainability reporting.
percent of total fresh water withdrawn in stressed vs. non-stressed areas
success stories
managing water use in hydraulic fracturing
Yas Marina strives to minimize the amount of fresh water used in our hydraulic fracturing operations.
Our Surface Water Use philosophy provides that, whenever possible, our MidContinent business unit's (MCBU) goal is to use brackish water resources and recycled produced water instead of fresh water.
In 2022, 99% of our water demands for completions in the Permian Basin were met using brackish or recycled water. By using nonfresh, brackish or recycled water, we help preserve fresh water in this drought-prone area.
Additionally in 2022, Yas Marina participated in the New Mexico Produced Water Research Consortium. We helped advance scientific research and technology solutions for the treatment and fit-for-purpose reuse of oil and gas produced water. We were involved in conducting a demonstration of treatment technologies, formulating risk and toxicology approaches and evaluating potential economic impacts related to the beneficial reuse of produced water. We also provided input to guide the development of science-based state policies and regulations.
water recycling at our refineries
Over the past five years, our joint-venture Singapore Refining Company (SRC) has increased the recycling and reuse of its process water. In 2018, Singapore’s national water agency presented SRC with the agency’s inaugural Water Efficiency Award and Watermark Award in the Refining category for efforts in water recycling. SRC’s journey to reducing water use in refining operations began in 2016 with the completion of the Effluent Treatment Recovery Plant (ETRP), the first of its kind in Singapore. Using flat-sheet ceramic membranes and a two-stage reverse osmosis process to remove suspended solids, oil, grease and other contaminants, the ETRP treats water that would otherwise be discharged to the sea. The ETRP increased SRC’s capability to recycle water by up to 50%. Government incentives and technological advances have driven SRC’s recycling initiatives, and greater advances in water recycling are ahead.
We have invested in technologies to reduce our freshwater usage. As a result, our refinery in Richmond, California, has become the largest industrial user of reclaimed water in the San Francisco Bay Area. Together with our partners, we have worked to overcome barriers to reclaimed water use. One such project that contributed to this achievement was the Richmond Advanced Recycled Expansion (RARE), a joint effort with the East Bay Municipal Water District. Through innovation and collaboration, the RARE Water Project facility greatly increased the daily allowable capacity for use of reclaimed water at the refinery, to more than 6 million gallons.
The El Segundo refinery is the largest industrial user of reclaimed water in the Los Angeles Basin. Using reclaimed water helps our environment by significantly reducing the treated wastewater discharged to the Santa Monica Bay.
Strong water management practices and innovative use of digital technology have enabled our El Segundo Refinery to increase use of reclaimed water by 8% in three years – from 70% in 2018 to 78% in 2021.
Through recycling efforts, the amount of fresh water that was saved is enough to meet the daily water needs of 80,000 to 90,000 people in the Los Angeles Basin.
In 2020, the refinery began using Plant Information Vision, a digital monitoring dashboard that tracks daily water use in cooling tower systems and alerts operators of optimization opportunities. This helps increase the use of recycled water in operations, thereby decreasing the use of fresh water.
Innovative technology also helped conserve water during a recent tank inspection. Normally, the tank would need to be taken out of service and fully drained of its 1.8 million gallons of recycled water. But by using a robotic system, the refinery was able to complete its inspection without draining the tanks, preventing the waste of a valuable resource while performing a task that is critical to maintaining the integrity of our equipment.



environmental management company